5 Ways to Improve Your Returns Processing
By Harold Baro, SIMOS Insourcing Solutions
The pandemic has caused a surge in eCommerce, which means the number of returned merchandise retailers see each year is growing. Americans returned $428 billion in merchandise to retailers last year according to the National Retail Foundation, which accounted for over 10% of retail sales in 2020.
If done incorrectly, returns processing can be an expensive and difficult business. But handling returns does not have to be a burden on your operation. Here are 5 quick ways to improve your returns processing operation.
1. Prepare your warehouse
Returns take up a lot of space and processing them efficiently means that they are just stuck wherever you have room. Take the time to plan out a space suitable for the process. Ideally, the space should be close to your inbound dock and have adequate staging areas to store and then process returns.
It should also be a place where supplies and equipment are easily located so that returns can be quickly processed and organized back into stock without disrupting your other warehouse operations. Putting thought into your returns space can cut down on extra steps and streamline the process.
2. Simplify
Take a look at your returns process. How many steps does it take to process a return and restock it? Are employees forced to take extra steps to find the barcode or return information? Streamlining and simplifying this process is an easy way to speed up your return times.
Many times the returns process is an afterthought and a process where man hours add up, costing additional dollars to re-handle. This is a work cell that if set up properly, and best practices are utilized, will yield savings and make a positive impact in your bottom line. Returns is an added cost, but there is no reason not to develop processes to keep those costs to a minimum while getting the returned items back into inventory for resale.
3. Plan for trash
Returns generate a lot of trash. Figure out the process for storing, sorting and removing trash and recycling. Doing so means that work is not hindered by a cluttered work area and nothing will get lost. An organized process leads to an efficient process.
4. Control restocking
Some of the best returns operations process returns and restock them within 24-36 hours. They can do this quickly because their restocking process is organized and straight-forward. Identifying and sorting items prior to putting them in picking locations can reduce the time required to restock. Having enough storage locations that are well labeled, means that restocking can be quickly completed while reducing your restock labor.
5. Partner with an output-based staffing company
With returns processing, it’s difficult to maximize efficiency and cost-savings when your operation is managed based on headcount. A staffing model where you manage your workforce based on output, not headcount allows you to manage staff based on the amount of returns that need to be processed or the inventory that needs to be shipped instead of worrying any people you need in your building.
With an output-based staffing strategy like SIMOS, your operation can reduce the number of steps in your production and increase efficiency quickly in your returns processing operation. Managing a workforce based on output means that you have budget certainty with your returns. During peak seasons or changes in eCommerce markets, this can become critical to not losing valuable time and money on returns processing.
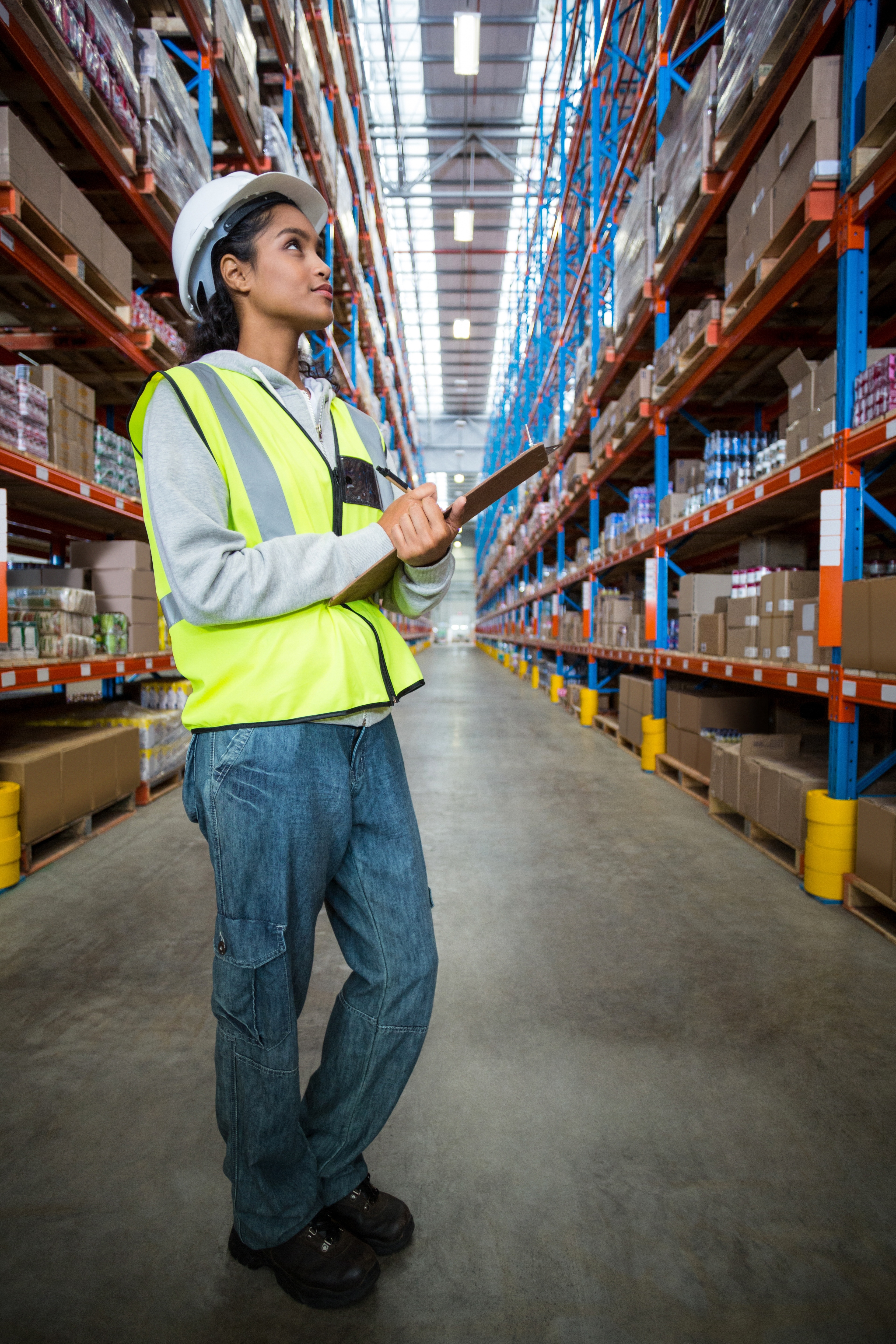
Harold BaroHarold Baro is senior vice president and general manager of SIMOS Solutions, a labor management firm that specializes in improving the ways organizations staff and manage high-touch environments by providing engineering expertise, a frontline workforce and management at a guaranteed fixed cost per unit while meeting quality and safety standards. He leads a core of certified engineers and experienced onsite workforce leaders who help optimize processes for budget certainty and increased efficiencies in distribution, fulfillment, reverse logistics and light manufacturing.