Tailor-made Circular Economy Logistics Hub (A case study by DB Schenker)
By Lucy Stephen Leifgen, DB Schenker
At DB Schenker, we are invested in closing the loop for a sustainable future – for our people, our customers, and the planet – by offering Circular Economy Logistics and value-added services, low carbon warehousing and eco-friendly packaging to help improve our customers as well as our ecological impact.
“The Circular Economy product is our commitment to realizing DB Schenker’s sustainability ambitions, while driving business value for our customers around the world.”
– Hessel Verhage, member of the Management Board for Contract Logistics, DB Schenker.
One such customer that has a strong commitment to sustainability and social responsibility is Konica Minolta, a leading provider of advance imaging and business solutions.
They recently partnered with DB Schenker to design, implement, and operate a purpose-built 5,200 square-meter reverse logistics distribution center in Poland.
Designing a reverse logistics warehouse
Designing a reverse logistics warehouse is a complex process that requires careful planning, attention to detail and a thorough understanding of the business requirements.
Konica Minolta needed a customized warehousing solution that included the solutions design, systems integration, implementation, and operations of its 5,200 square-meter distribution warehouse with an in-built Technical Center for installing software systems in printing devices as well as the handling of returns, repairs, and refurbishment of those devices.
To maintain business continuity with its customers and keep its highly skilled workforce, Konica Minolta engaged DB Schenker to locate, design and set up a new highly sophisticated distribution center within proximity to its current operations, all within a strict timeline.
Customized solutions design
Our team consulted with the customer to identify key business challenges, and design a customized solution that delivered upon Konica Minolta’s business requirements.
1. Designing a custom-built Technical Center within the warehouse.
The first key challenge for the customer was to include the design of a Technical Center within the 5,200 square meter distribution warehouse. The center is a separate space within the warehouse dedicated to the work of Konica Minolta specialists installing the software system in printers as well as the repairs and refurbishment of returned printing devices. The space needed to be temperature controlled, with additional lighting and dust extractor for the stations within the Technical Center. The design also catered for the provision of value added services and management of just-in-time delivery of the printers to the Technical Center. Each printer is unpacked with transport wheels and paper trays installed prior to being delivered just-in-time to the Technical Center.
2. Finding an attractive location for business continuity.
To maintain business continuity for their customers as well as keep their specialized technicians that are directly employed by Konica Minolta to perform refurbishment, repairs and systems updates to the printers, DB Schenker was instructed to find an attractive location within proximity to Konica Minolta’s current operations. It was important for Konica Minolta to keep their team of technicians without drastically changing their work location. The challenge was to find a suitable, accessible location near the existing Technical Center that would meet the client's requirements and be available in a timely manner for implementation.
3. Tight turn-around times to guarantee business continuity.
A critical success factor was DB Schenker’s ability to guarantee operations would start on time and ensure business continuity for Konica Minolta’s customers. DB Schenker designed, implemented, and will begin operations as scheduled. The customer outlined this as a key risk factor early on in our discussion and therefore it was important for DB Schenker to provide and deliver upon the tight-turnaround times.
4. An expert team of solutions designers created the right combination of process, systems, and warehouse design.
As part of the design, a team of solutions designers identified and combined two key processes within the warehouse: (1) manage new and used printers, and (2) manage consumables and parts such as toners, small parts and cables.
A pick-and-pack system was designed and installed for both larger printers as well as the smaller items. Similar to pick-and-pack systems in an e-commerce warehouse, our Solutions Design team included a system to manage the supply process of consumables for Konica Minolta's leasing customers.
The combination of these two independent processes was key in creating an effective operation. Throughout the consulting process, our team delivered 3D visualization and a flythrough of the warehouse that made it easy for Konica Minolta to decide on the solution they wanted.
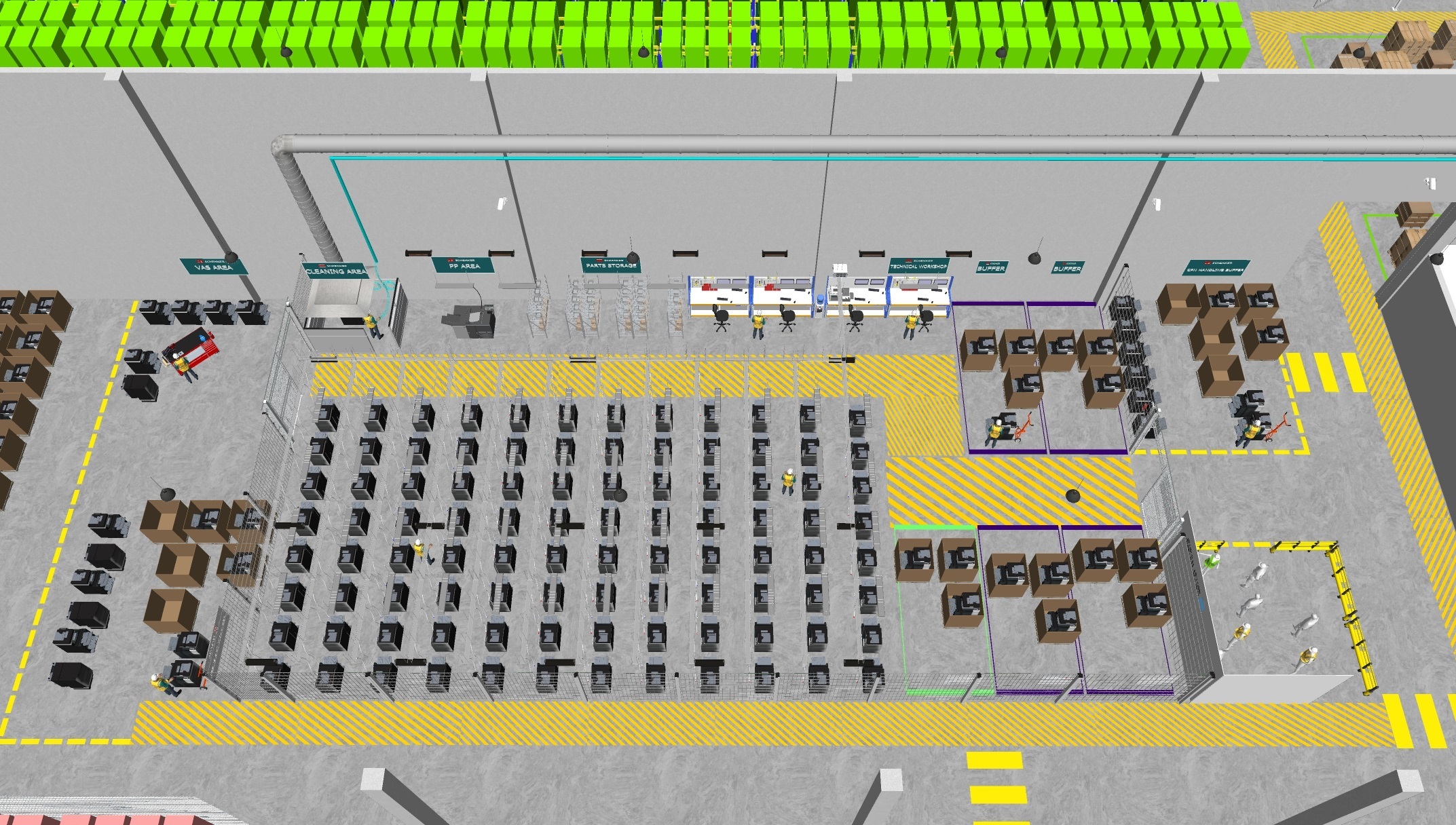
SketchUp Flythrough of the DB Schenker Konica Minolta Circular Economy Logistics distribution center in Poland
5. Integrate multiple IT systems and ERP software for a smooth operation.
A key component in bringing the distribution center into operations is the IT integration and set up between DB Schenker, Konica Minolta and its local carriers that deliver the printers to its customers. The warehouse operations are carried out on the DB Schenker IMI WMS System and is integrated with Konica Minolta’s Enterprise Resources Planning (ERP) software and systems used by other local carriers responsible for the distribution of the printers.
Operating a reverse logistics distribution center
The 5,200 square meter warehouse is expected to store approximately 4,500 new and used printers and 2,000 pallets of consumables. Every day an estimated 120 printers and around 500 packages of consumables are expected to leave the warehouse.
A specially designed Technical Center located within the warehouse features stations dedicated to the installation of software systems within printers as well as the handling of repairs and refurbishment of returned printing devices. The Technical Center is a temperature-controlled space fitted with additional lighting and dust extractors. Konica Minolta has employed specialist workers who will perform the refurbishment, cleaning, quality control, systems, and software updates on the printers.
While DB Schenker is contracted to run the operations of this warehouse, ensuring the printers are properly received from the inbound station, unpacked, transport wheels and paper trays installed on each printer, and are delivered just-in-time to the Technical Center.
As part of the operations, our team has constructed two main processes within the warehouse to manage printers and consumables.
From inbound to the Technical Center through to the final stages of preparation for outbound, DB Schenker ensures the smooth handling of Konica Minolta’s printers and consumables. Our teams provide value-added services, maintains the IT systems, conducts quality control, and manage the serial numbers of printers and parts that either arrive from the factory or are returned from Konica Minolta’s customers post-leasing. We ensure devices are prepared for transport, secured and proper documentation and processes are followed prior to releasing the items to local delivery providers.
About DB Schenker's Circular Economy Logistics
DB Schenker is a diamond member of the RLA. The company has the know-how and experience in returns and reverse logistics through operations for key customers especially in the electronics industry. Annually, DB Schenker processes millions of returns of electronic devices and offers modular reverse management operations to provide one-stop-shop for its customers.
DB Schenker offers Reverse Logistics and Value-Added Services in their warehouses to contribute to a circular economy. The current offer focuses on returns initiation, returns processing, and repairs processing solutions for electronics and consumer and retail industries, and is planning to expand its horizons to other industry sectors.
Lucy Stephen LeifgenLucy Stephen Leifgen is a Customer Experience and Marketing Manager in the Contract Logistics business at DB Schenker. DB Schenker is one of the world’s leading global logistics providers — supporting industry and trade in the global exchange of goods through land transport, worldwide air and ocean freight, contract logistics and supply chain management. Lucy has extensive marketing and communications experience in the European and Asia Pacific markets. At DB Schenker, Lucy is focused on working with customers and partners in delivering strategic communications on contract logistics and supply chain management.