SQRL Code Pilot Project White Paper
By Bruce Brown,
Product labeling is an important aspect of many business processes. In most cases, each of these processes—involving labeling, are managed through separate systems that are often incompatible. Some companies are adopting labeling systems that are integrated and even connect with corporate ERP and PLM environments. Regardless, the art of designing and producing labels is complicated, time consuming and expensive. There are numerous applications that require labeling:
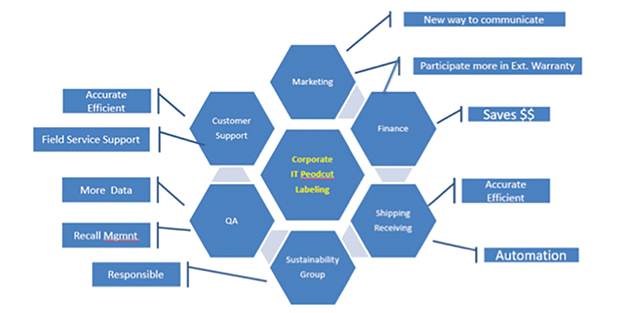
Most companies are organized around functions. These functional groups are often autonomous with clearly defined roles and responsibilities. Labeling is one of those functions that, correctly so, is found in each corporate division, though IT usually becomes the coordinator of all labeling functions since it is the hub for storing the labeling contents.
Label design is often shifted to IT since they manage the data libraries. Still, stand-alone systems, for instance, in warehousing, may have hundreds of printers producing application specific labels.
img3
For a tier one manufacturer the management of this task can be daunting. A recent case study published about Siemen’s recent up- grade to an integrated labeling management system provided a fascinating insight into the complexity of the labeling process in a major company.
Recently Siemens adopted NiceLabel Centralized Labeling suite to modernize their product labeling environment. The case study shows an ROI in four months. It also showed Label print time reduced from 8 seconds to 300 milliseconds. The scalable solution are used at 22 sites with a total of 1,200 printers at the time of the report. It is still being rolled-out as a best practice throughout Siemens.
Still most products bear multiple labels. Many electronic products have internal model numbers, serial numbers, UPC codes, Certification and compliance labels. They may also have special channel specific labels. Many of these labels are also printed on the product packaging, and again on the cartons and even the pallets. Pick and place labeling machines are programmed at the end of the manufacturing line and the packaging line to properly identify the product.
Logistics also has a labeling process, as does reverse logistics. RMA authorizations are often paperwork that travel with returned products and sometimes get separated from the returned items. Many systems are now attaching labels to reduce the disruptions instigated by lost paperwork.
This is unavoidable—especially as many of these labels are legislated and required by law. The labeling requirements vary according to the industry with food, pharma and electrical products bearing the bulk of the regulations—and justifiably so for safety reasons.
What if the labeling process could be stream-lined? Modern optical scanning technology has evolved to allow thousands of characters of data to be readable by smart phones as well as industrial scanners. Using off-the-shelf QR codes, a single label can contain up to 4000 characters. Today, most QR codes only contain about 100 characters. Why? Because there has been no standardized field delimiter; meaning that the QR code has a single field.
The Reverse Logistics Association’s Standards Committee has addressed this by the establishment of an open standard—endorsed by ANSI, MH10.8.2.12N . This standard labeling protocol offers a dictionary of field titles, including such items as serial numbers, UPC codes, and compliance information, together will a defined field delimiter that allows multiple fields of information to be contained in a single label. A field delimiter is a special character that is inserted to identify where one field, such as a Name field, ends and the next field, such as an Address field begins. In-fact, with the 12N protocols, unlimited data can be accessed.
Using 12N labeling protocols, ONE LABEL can do it all!
Because each field can be independently encrypted and because each field can be a different language or currency, this is a global solution that can be adjusted to accommodate any labeling requirements or compliance issues. Some fields can be scanned by consumers using smart phones. Encrypted fields may be accessed by logistics professionals with the appropriate key-codes.
Today, labels are usually generated through some kind of XML system that feeds the data into a special CAD program that produces the labels. The XML data is interfaced to the ERP and/or PLM system and into a library of label artwork. Some labels are generated as part of a Workflow process on an ad hoc basis. Both processes can be adapted to use the 12N protocols.
What would be the result of this? There would be one label on the product, one label on the packaging, one label on the carton and one label on the pallet. The returns process could be adapted to send one label for RMA authorizations that could be attached directly to the item (no more lost paperwork). Label print time would be further reduced. None of the workflow processes would need to be changed.
Because there is so much capacity on this label, marketing will have a field-day. There is so much more we can tell our consumers.
Adopting the 12N protocols needs to begin with a pilot project. While there are numerous applications that can be enabled with this system, it needs to begin with a simple proof of concept.
Examples
Presales support:
Objective: Make it easier for potential customers to access information about the product.
Metric: 1) do products with new label sell more in same store? 2) do we get more pre-sales support calls? 3) are there fewer product returns with reason being “wrong product?”
Return support:
Objective: Reduce the number of returns with incomplete parts.
Metric: 1) based on history, does adding content “list of items to be returned” on the product reduce the number of incomplete returns? 2) is the returns triage process quicker as a result? 3) Are fraud returns reduced with this extra process?
Product registrations
Objective: Increase the percentage of consumer product registrations
Metric: 1) by putting auto-logon to product registration, do more consumers register? 2) do we collect more accurate or more complete information compared to post cards?
Repair and Refurbishing:
Objective: Create an optically scannable digital toe-tag that travels with the returned product. To relabel a Refurbished Product with new warranty information and repair history.
Metric: More accessible customer support with fewer calls to OEM. Easier access to product repair history.
Less separated paperwork in workflow.
Each of these examples requires knowledge of the base line information. The baseline data should include data related to specific channels. Each pilot project should be timed to record two inventory shipments to each channel location. These shipments can be sequential or separated by a defined time.
An effective pilot project depends on good planning. Measurable metrics will provide an objective evaluation. Change for change sake is costly and all changes need to be justified. Ultimately, all process enhancements or modifications must save money: sometimes the savings are indirect. Saving time, adding more automation, or reducing costs are obvious. Increasing data collection, improving customer promotional scores are less obvious, but equally as valuable.
The cost savings and benefits derived from the adoption of Standard QR Labels crosses most business processes. Therefore, the ideal Pilot Project has input from all business units, creating a cross matrix team.
A brainstorming session about potential applications can and will create some excitement about the potential of this approach to product labeling. However, the Pilot Project should have a more modest goal. After the brainstorming session, the ideas should be prioritized. For a successful pilot, only TWO clearly defined objectives with metrics should be selected.
The Reverse Logistics Association is currently seeking companies interested in mounting a pilot project. If your company would like to be on the leading edge of this project please let us know. You can reach us at SQRL@rla.org and join our Standards Committee. For more information about the 12N codes, visit www.rla.org/sqrl
Bruce BrownInforMission Solutions, LLC provides system support for creating and scanning RLA / ANSI SqrL-compliant labels.
After 9 years in various management roles at Apple, Bruce served as CIO for two $1B+ corporations, founded a B2B SaaS (business to business software as a service) company and ran a multi-channel e-commerce company. Bruce now serves as InforMission's CEO.