Revolutionizing Reverse in the Mobility Industry
By Mark Brausa, Ingram Micro Commerce & Lifecycle Services
A Landscape Primed for Growth
The logistics industry has long focused on forward logistics services and distribution, deprioritizing progress in reverse logistics management.
The combination of continued growth in forward logistics, a need for 3PLs to ship directly to consumers in addition to stores, and notably — take-back programs that collect used devices with high remarketing value — is creating more demand for accurate and efficient reverse logistics solutions.
To better emphasize the growing demand, it is helpful to understand these trends (IDC, B-Stock):
- By 2022, the secondary market for mobile devices is projected to exceed $57 billion.
- It will exceed 290 million devices and have doubled in size from 2017, representing a CAGR of 14.9%.
- As many as 40-50% of mobile devices (117-146 million units) will be traded back to carriers for repair, refurbishment and resale.
- Secondary market growth is exceeding that of the primary market.
With consumers buying new mobile devices less often, repair volumes are increasing and carriers require a strong ROI. OEM and repair center SLAs are evolving to include faster diagnostic testing, more sophisticated grading, improved integration between partner and carrier systems, and a higher level of functional testing. Performance indexes, score cards and overall quality improvements have also become standard.
With the push to fund 5G networks, carriers are also looking to improve cash flow. There are two strategies for maximizing value: fast movement through the refurb processes, and grade skipping. The former can be accomplished through system efficiency and the latter relies on polishing and buffing to improve cosmetic grading.
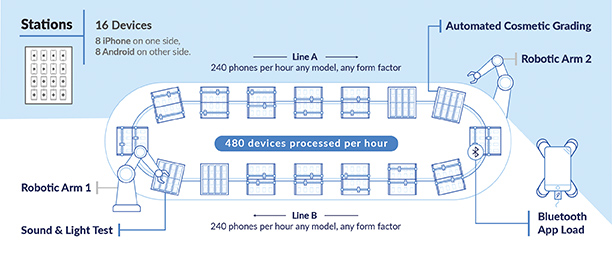
Ingram Micro is Revolutionizing Reverse
Using automation and metric-based quality, we’re transforming the way RLR for mobile devices is done. We’re building a complex, automated system called “REV” that combines software and hardware to speed up the rate of device grading and improve cost-effectiveness and accuracy.
Recognizing that repetitive action, speed and precision are key factors in the grading process and that single-device robotic stations are impractical due to issues of scale, we designed REV to be flexible. The end-to-end solution will integrate, manage and automate various line-optimized diagnostic hardware components using technology to achieve high-throughput, flexible and ROI-optimized diagnostics. REV will also perform highly-accurate and speedy cosmetic grading on mobile phones — an exclusive capability designed and built by Ingram Micro’s engineers.
Now in its final stages of development, REV will be able to process over 480 devices per hour, equating to over 1.9M devices per year — on a single machine. This makes a 500% improvement time on current mobile device processing times.
The system will provide:
- Concurrent processing of multiple devices.
- Mobile device warehouse diagnostics line optimization via software processes.
- The ability to control hardware from a central business logic management layer to ensure customer requirements are consistently controlled.
- A process engine that runs complex, reactive scripts over dozens of devices concurrently.
- Flexible business logic management of process flows, controlled via real-time hooks with 3rd-party policy configurations.
- Policy-based routing of DUTs after final test completion.
- Individual device status throughout the entire process.
- Real-time monitoring dashboards of the entire floor, lines and stations to ensure customer SLAs are always met.
- An Enterprise Resource Planning (ERP) server reporting with all data relevant to testing.
Testing Capabilities
REV will enable up to 100 different tests to be selected for processing on each device and can automatically detect which tests are relevant to run on a given device. Cosmetic damage, surface defects, pixel-level display defects and counterfeit display parts are all within the realm of detection. It can also classify the texture and material of packaging, complete functional tests and classify/grade smart devices.
Other benefits:
- No pre-charging of devices is required.
- No presorting by customer or model device type needed.
- Automatically adjusts to the form factor of the device and inserts the correct connectors into the ports of any Android or iOS device.
Addressing Future Needs, Today
Reducing costs and improving quality for our customers are central to REV’s value. In addition to handling high volume spikes without increasing expenses, the system delivers significant process efficiencies (faster device processing and labor training) that result in more devices graded in a shorter time period. In terms of quality, customers can expect to receive information far beyond “there’s a scratch on the phone.” Instead, REV will report the depth of the scratch and how it can be repaired.
REV’s launch is just the first step in our mission around Revolutionizing Reverse. Stay tuned for more!
To keep up to date with REV’s launch and future innovations, visit www.ingramicroservices.com/REV.
Mark BrausaMark Brausa has worked in the wireless industry for over 20 years, both on the carrier side and the supplier side of the business. For the past 15 years, he’s focused on reverse logistics and repair, and prior to his current role, was part of the leadership team that built the largest phone repair business in North America.